- Our Value Creation Model
- Our Strategic Priorities
- Stakeholder’s Engagement
- Materiality Assessment
- Branding Stories
- Manufacturing Excellence
- Digitisation
- Technology, Product & Process Innovation
Creating Value with a
Sustainable
Business Model
Our Company’s value creation model thrives on the efficient and effective utilisation of our resources. This section of the Report outlines our initiatives to optimise and expand our resource pool, which is crucial for generating sustainable value for our stakeholders. At Mahindra Accelo, we’re recognised for our agility, consistently evolving our business models to match industry needs and seize business prospects. The snapshot below showcases the varied business verticals within which our Company operates.
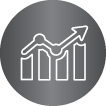
Financial Capital
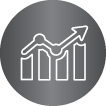
- Net Fixed Assets as of FY 2023-24 ₹ 719.45 crore
- Net Working Capital as of FY 2023-24 ₹ 534.83 crore
- Net Worth as of FY 2023-24 ₹ 1,104.77 crore
- Net Debt to EBITDA Ratio 1.23
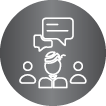
Manufactured Capital
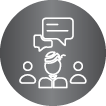
- Total No. of Steel Service Centre Facilities 11
- Automotive Recycling Centres 7
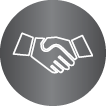
Social and Relationship
Capital
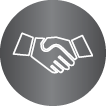
- Amount Spent on Community Development Projects ₹ 3.57 crore
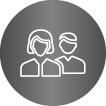
Human Capital
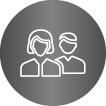
- Total No. of Employees 407
- Total No. of Contractual Workers 719
- Total Training Hours 14,187
- Employees Trained (Person Hours) 10.47 days
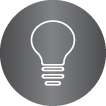
Intellectual Capital
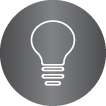
- Digitisation Efforts at Mahindra Accelo 33 Projects
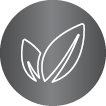
Natural Capital
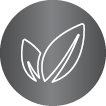
- Energy Consumption 32,137 GJ
- Renewable Energy Consumed 2,816 GJ
- Total Water Consumption 40,686 M3
- Natural Raw Materials Procured 5,00,094 tonnes
Purpose
Drive positive change in the lives of our communities. Only when we enable others to rise will we rise #TogetherWeRise.
Enabling Stakeholders to Rise
- Building a great place to work
- Fostering an inclusive development
- Making sustainability personal
Rejuvenating the Environment
- Achieving carbon neutrality
- Becoming water positive
- Ensuring no waste to landfill
- Promoting biodiversity
Building Enduring Business
- Grow green revenue
- Mitigate risk, including climate risk
- Make supply chain sustainable
- Embrace technology and innovation
- Enhance brand equity
Our Business
- Mobility components
- Energy components
Manufacturing Process
- Procuring from steel mills
- Processing/manufacturing various components for different applications & value-added services
- Finishing products
- Delivering to our customers
Financial Capital
- Net Revenue ₹ 4,564.94 crore
- EBITDA ₹ 293.15 crore
- Profit after Tax ₹ 157.11 crore
Manufactured Capital
- Volumes (in tonnes) 5,06,860 tonnes
Social and Relationship Capital
- Customer Satisfaction Index 80
- No. of People Benefitting from Community Investments 11,591
Human Capital
- Great Place to Work Rank 44th
- Women in Workforce 5%
- Workforce Covered through Unions 11.06%
Intellectual Capital
- No. of New Digital Initiatives Planned for FY 2024-25 40 Projects
Natural Capital
- Water Recycled 7%
- Scope 1 + 2 Emissions 4,375 MTCO2.
Charting the Sustainable
Roadmap for
Long-Term
Progress
At Mahindra Accelo, we spearhead the decarbonisation revolution through the provision of sustainable products and vehicle recycling to foster a resilient and sustainable world. Our Company aims to expedite the decarbonisation process and deliver lasting value. Across all our businesses and products, our focus remains on advancing decarbonisation efforts and nurturing a sustainable future for all stakeholders. Additionally, Mahindra Accelo is at the forefront of paving the way towards a carbon-neutral future.
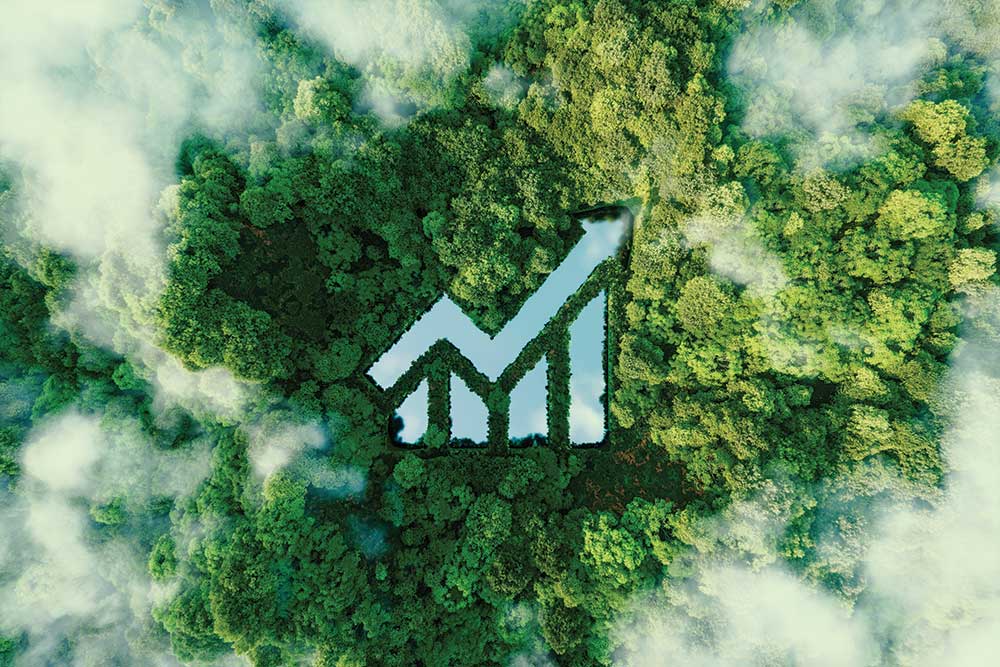
Become a Tier 0.5 Auto Component Player for 4-Wheeler OEMs
- Entering the auto component space with an investment in India’s first 1500-ton progressive stamping line for manufacturing auto components.
- Leveraging our Group DNA, we are driving technology and innovation in the auto component sector. We have invested in India’s first 3000-ton transfer press to manufacture Class B components.
- Investing in a world-class tandem press line to manufacture skin panels / Class A components. These lines can also stamp aluminium, positioning us for a seamless transition to other metals in the future.
- Implementing world-class automated robots to manufacture critical assemblies for OEMs, aiding them in achieving high safety ratings.
- Expanding capacities in processing lines and, alongside the aforementioned new investments, planning to diversify and cater to major auto OEMs in India.
Lead the EV Transition in India by Supplying Critical Components
- Supplying stamped BiW components to EVs. All our lines can stamp Advanced High Strength Steel (AHSS)/High Strength Steel (HSS), preparing us for the EV transition.
- Expanding our world-class setup to manufacture motor cores for EVs & Hybrids. We can supply motor cores for E-2-wheelers, E-3-wheelers, and E-4-wheelers & Hybrids.
- Investing in one of the best MSP presses to manufacture motor cores from high-grade steel with a 0.2 mm thickness is essential for E-4-wheelers to improve efficiency.
- Developing technology to manufacture full battery boxes for EVs. We have already created prototypes for aluminium top and bottom covers for the EV battery box. Our presses are capable of stamping aluminium, positioning us to manufacture top and bottom covers for the battery box.
Gain Significant Market Share in Distribution Transformer Components
- Leveraging our capabilities in the power transformer component space, we have established world-class distribution lines at various locations across India, enabling us to enter the distribution transformer sector. This move is particularly significant given the current dominance of unorganised players in this area.
- Expanding our presence across India allows us to be closer to customers and provide just-in-time (JIT) service.
- Our operations in the power sector are already established in seven different locations, including a global presence in Sharjah & Indonesia. Looking ahead, we are keen on further expanding our export base by supplying from our global locations
- We are also expanding capacities across India to prepare for the anticipated growth in renewable energy and EV charging infrastructure. This growth trajectory is expected to drive expansion in the distribution transformer industry.
Remain Largest Organised Vehicle Recycler in India
- Already present in 42 cities across India, making us the largest organised vehicle recycler in the country.
- Leveraging the network, we plan to expand to over 100 cities in the near future
- Developed one of the most advanced Lead Management Systems (LMS) to efficiently manage leads from the sourcing stage to the complete vehicle recycling process on a digital platform
- Dedicating to driving a circular economy by recycling end-of-life vehicles
Fostering Relationships
for Shared
Success
At Mahindra Accelo, our business model’s successful operation relies on multiple stakeholders’ input. We actively engage with these stakeholders, understanding that nurturing healthy and mutually beneficial relationships is vital for sustaining our efforts in value creation.
Shareholders
Customers
People
Suppliers
Communities and Our Environment
Engagement Philosophy
We are committed to transparent engagement with shareholders to ensure a clear understanding of our Company’s performance across all areas, including strategic and financial performance and environmental, social, and governance aspects.
Engagement Approach
We encourage year-round engagement and transparency in all aspects of our business. Our CFO and Finance team regularly engage with investors to explain our investment proposition, ESG performance, and current performance. We also provide timely responses to shareholder queries.
Key Discussion Topics
- Business strategy and execution plans
- Consistency in financial performance and returns
- Sound corporate governance
- ESG priorities and strategy
Our Responses
- Focussed decisions and actions
- Strong delivery of financial performance
- Adherence to the highest standards of transparency and integrity
- Establishment of a best-in-class Board with strong governance mechanisms
- Focus on ESG with transparent and detailed disclosures
Engagement Philosophy
As a customer-centric company, we prioritise adapting to rapidly evolving consumer needs. Our sustainable growth journey hinges on delivering quality products and expanding our consumer base.
Engagement Approach
Our sales and marketing teams actively engage with our focus customers to gauge our performance and identify new opportunities. Additionally, we conduct thorough market research to glean insights into emerging trends and consumer preferences.
Key Discussion Topics
- Offering a broad portfolio providing ample choices across categories
- Understanding customer requirements and pain points
- Promoting responsible and inclusive marketing practices
Our Responses
- Collaborating with customers to find the most effective solutions
- Increasing investment in product development
- Upholding high-quality manufacturing, sourcing, and environmental standards
- Offering products at multiple price points to deliver tangible value
- Developing product and technology roadmaps based on emerging trends
Engagement Philosophy
Our Company’s workforce is our most valuable asset, and their health, safety, and well-being are our top priorities. We value engaged teams and strive for all colleagues to be committed to our vision.
Engagement Approach
At our Company, we prioritise effective communication, primarily from line managers to their teams. We conduct regular town halls with senior management to ensure messages are cascaded and discussed at all levels. Additionally, we track the performance of all team members and guide their growth and excellence.
Key Discussion Topics
- Advocating for health, safety, and well-being initiatives
- Embracing opportunities for learning and development
- Fostering a sense of belonging and purpose
- Embracing diversity and inclusion=
Our Responses
- Implementing smart recruitment methodologies
- Enhancing retention and succession planning strategies
- Increasing engagement initiatives with the workforce
Engagement Philosophy
Our suppliers play a critical role in our supply chain, and we prioritise working in partnership with them to enhance the strength of our supplier base.
Engagement Approach
Our Company conducts regular business reviews with our key suppliers throughout the year to assess their performance and gain insights into their challenges, issues, and concerns.
Key Discussion Topics
- Adhering to the code of conduct
- Evaluating supplier performance
- Addressing component shortages and implementing mitigation strategies
Our Responses
- Implementing integrated business planning
- Providing supplier training programmes
- Consolidating our supplier base to focus on high quality
- Collaborating with distributors to secure long-term demand for key components
Engagement Philosophy
We actively engage with the communities in our operational areas to foster trust and drive initiatives related to health, skill development, education, and environmental conservation.
Engagement Approach
Mahindra Accelo’s focus areas include supporting local causes and addressing community needs through impactful interventions. Our Company also prioritises environmental stewardship by minimising our ecological footprint.
Key Discussion Topics
- Understanding community concerns and aligning with employee efforts for more significant impact
- Sharing our sustainability strategy with communities
Our Responses
- Conducting annual reviews and checks
- Implementing emission reduction plans and targets
- Adopting water conservation practices
- Incorporating upliftment programmes for marginalised communities
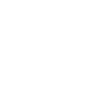
Engagement Philosophy
We are committed to transparent engagement with shareholders to ensure a clear understanding of our Company’s performance across all areas, including strategic and financial performance and environmental, social, and governance aspects.
Engagement Approach
We encourage year-round engagement and transparency in all aspects of our business. Our CFO and Finance team regularly engage with investors to explain our investment proposition, ESG performance, and current performance. We also provide timely responses to shareholder queries.
Key Discussion Topics
- Business strategy and execution plans
- Consistency in financial performance and returns
- Sound corporate governance
- ESG priorities and strategy
Our Responses
- Focussed decisions and actions
- Strong delivery of financial performance
- Adherence to the highest standards of transparency and integrity
- Establishment of a best-in-class Board with strong governance mechanisms
- Focus on ESG with transparent and detailed disclosures

Engagement Philosophy
As a customer-centric company, we prioritise adapting to rapidly evolving consumer needs. Our sustainable growth journey hinges on delivering quality products and expanding our consumer base.
Engagement Approach
Our sales and marketing teams actively engage with our focus customers to gauge our performance and identify new opportunities. Additionally, we conduct thorough market research to glean insights into emerging trends and consumer preferences.
Key Discussion Topics
- Offering a broad portfolio providing ample choices across categories
- Understanding customer requirements and pain points
- Promoting responsible and inclusive marketing practices
Our Responses
- Collaborating with customers to find the most effective solutions
- Increasing investment in product development
- Upholding high-quality manufacturing, sourcing, and environmental standards
- Offering products at multiple price points to deliver tangible value
- Developing product and technology roadmaps based on emerging trends
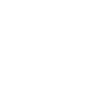
Engagement Philosophy
Our Company’s workforce is our most valuable asset, and their health, safety, and well-being are our top priorities. We value engaged teams and strive for all colleagues to be committed to our vision.
Engagement Approach
At our Company, we prioritise effective communication, primarily from line managers to their teams. We conduct regular town halls with senior management to ensure messages are cascaded and discussed at all levels. Additionally, we track the performance of all team members and guide their growth and excellence.
Key Discussion Topics
- Advocating for health, safety, and well-being initiatives
- Embracing opportunities for learning and development
- Fostering a sense of belonging and purpose
- Embracing diversity and inclusion=
Our Responses
- Implementing smart recruitment methodologies
- Enhancing retention and succession planning strategies
- Increasing engagement initiatives with the workforce

Engagement Philosophy
Our suppliers play a critical role in our supply chain, and we prioritise working in partnership with them to enhance the strength of our supplier base.
Engagement Approach
Our Company conducts regular business reviews with our key suppliers throughout the year to assess their performance and gain insights into their challenges, issues, and concerns.
Key Discussion Topics
- Adhering to the code of conduct
- Evaluating supplier performance
- Addressing component shortages and implementing mitigation strategies
Our Responses
- Implementing integrated business planning
- Providing supplier training programmes
- Consolidating our supplier base to focus on high quality
- Collaborating with distributors to secure long-term demand for key components

Engagement Philosophy
We actively engage with the communities in our operational areas to foster trust and drive initiatives related to health, skill development, education, and environmental conservation.
Engagement Approach
Mahindra Accelo’s focus areas include supporting local causes and addressing community needs through impactful interventions. Our Company also prioritises environmental stewardship by minimising our ecological footprint.
Key Discussion Topics
- Understanding community concerns and aligning with employee efforts for more significant impact
- Sharing our sustainability strategy with communities
Our Responses
- Conducting annual reviews and checks
- Implementing emission reduction plans and targets
- Adopting water conservation practices
- Incorporating upliftment programmes for marginalised communities
Mapping Material Aspects
with Impactful
Strategies
Materiality refers to identifying the most significant aspects for reporting, enabling concise and effective communication. This approach helps stakeholders make informed decisions with ease and clarity.
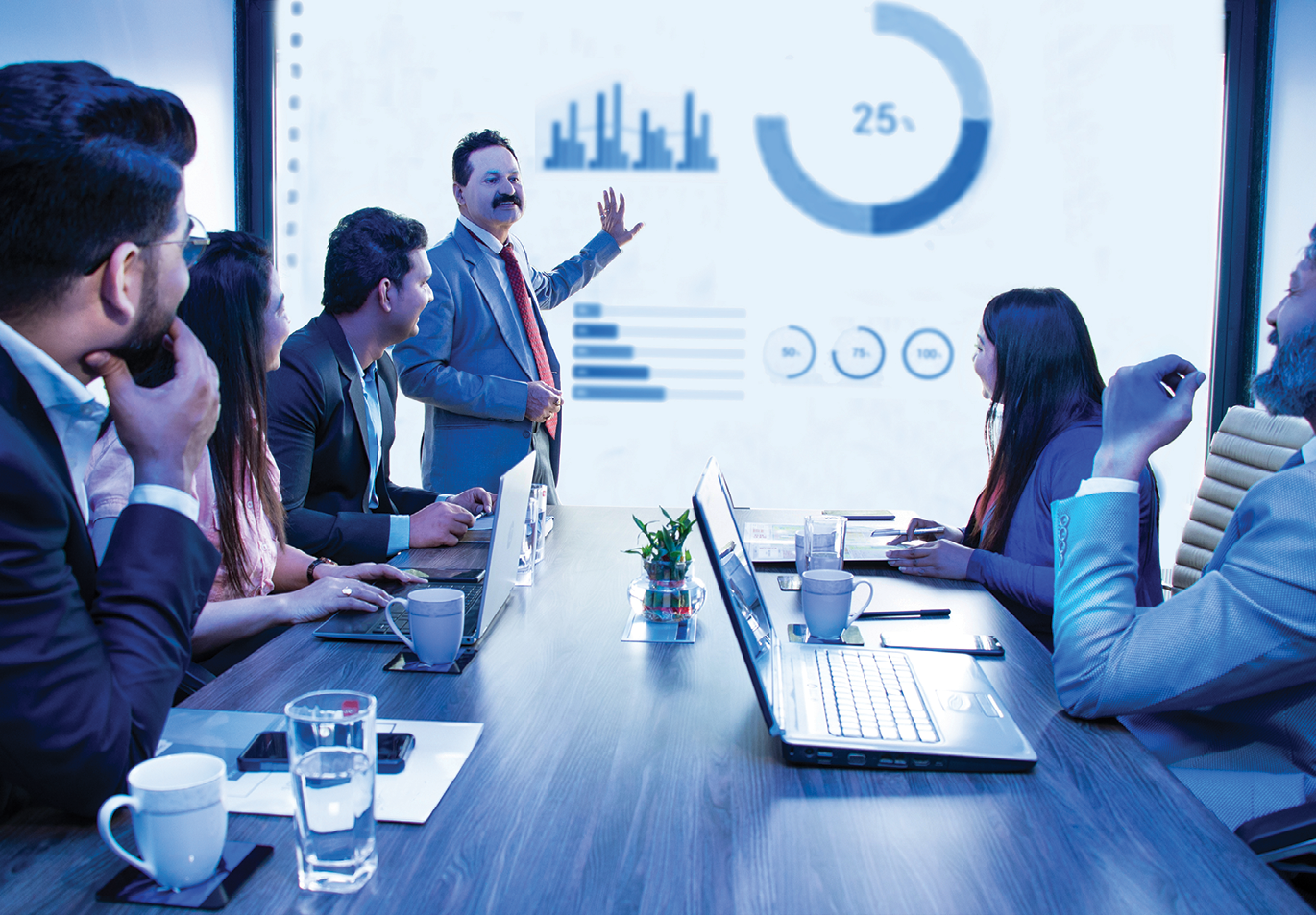
Materiality Assessment Process
Define purpose, scope, and stakeholders
Identify potential topics
Stakeholder engagement survey
Response analysis
Senior management interaction for prioritisation of issues
Establish materiality matrix
Material Issues
- 1. Energy Management
- 2. Circular Economy
- 3. Corporate Governance and Compliance
- 4. Customer Relationship Management
- 5. Occupational Health and Safety
- 6. New Growth Opportunities, Brand Reputation and Business Continuity
- 7. Digitisation, Data Protection and Privacy
- 8. Risk and Crisis Management
- 9. Labour Management
- 10. Economic Performance
- 11. Human Rights
- 12. Technology, Product and Process Innovation
- 13. Employee Attraction and Retention
- 14. Climate Change
- 15. Operational Eco-efficiency
- 16. Employee Training and Development
- 17. Supply Chain Sustainability
- 18. Fair Employment
- 19. Diversity and Inclusion
- 20. Community Development
- 21. Air Emissions
Amplifying Brand
Prominence with
Visibility
and Impact
Mahindra Accelo undertook several strategic initiatives throughout the fiscal year to strengthen our brand presence and reach a wider audience. These initiatives encompass a diverse array of marketing channels, each meticulously crafted to resonate with our target demographics and amplify our brand message. Below, we outline the key brand initiatives implemented during the reporting period:
Amplifying Reach
Our magazine advertising campaigns have successfully penetrated the print media landscape, reaching an impressive readership of 29,97,000 individuals. These ads have effectively communicated our brand values and product offerings to a discerning audience through captivating visuals and compelling content.
Enhancing Brand Representation
Complementing our magazine ads, our comprehensive product portfolio brochure serves as a tangible representation of our commitment to excellence. Designed to showcase the breadth and depth of our offerings, this collateral piece provides potential customers with invaluable insights into our range of products and services.
Strengthening Direct Engagements
Embracing the digital age, we have leveraged the ubiquitous platform of WhatsApp to engage with our customers on a more personal level. Our WhatsApp marketing initiatives have fostered meaningful connections through targeted messaging and interactive content, driving brand awareness and customer loyalty.
Reinventing the Brand
With a strategic focus on online visibility, our display advertising campaigns captivated digital audiences and have also reached the masses, generating widespread awareness of the brand Mahindra Accelo and our products. By harnessing the power of eye-catching visuals and compelling copy, these advertisements have effectively captured the attention of potential customers, driving traffic to our digital assets and generating valuable leads.
Dominance
Recognising the pivotal role of social media in modern marketing, we have cultivated a dynamic presence across various social platforms. From engaging content to interactive campaigns, our social media initiatives have fostered a vibrant community of brand advocates and loyal followers, facilitating meaningful conversations and driving brand engagement.
In conclusion, our brand initiatives reflect our unwavering commitment to innovation, creativity, and customer-centricity. By embracing a multi-channel approach and harnessing the power of both traditional and digital mediums, we have successfully elevated our brand presence, expanded our reach, and solidified our position in the market landscape. Looking ahead, we remain dedicated to pushing the boundaries of brand excellence and delivering unparalleled value to our stakeholders.
Mahindra Accelo remains steadfast in its mission to inspire, innovate, and empower, and we are confident that our brand initiatives will continue to drive growth and success in the years to come.
Achieving Excellence with
Quality and
Efficiency
Mahindra Accelo uses a holistic approach that integrates continuous improvement, innovative strategies, and a commitment to customer satisfaction to achieve excellence in quality and efficiency. This focus on efficiency is essential for our long-term success, allowing us to stay ahead in a competitive market.
We place paramount importance on our manufactured capital, which comprises state-of-the-art production facilities, cutting-edge technology, and a skilled workforce. This capital forms the backbone of our operations, enabling us to deliver exceptional operational performance and maintain our competitive edge in the industry.
Building a Foundation for Excellence
At Mahindra Accelo, we have embraced the 6S strategy as a cornerstone of our operational excellence journey. By integrating 5S principles with a focus on safety, we have created a systematic approach to enhance efficiency and safety across all our operations. This strategy involves dividing our factories into zones with clear ownership, ensuring adherence to a comprehensive 5S manual, and conducting regular red tag campaigns. We conduct regular 5S audits, with scores integrated into our Balanced Score Card (BSC)/Key Result Area (KRA) for management staff. To strengthen the 6S culture, we have continued to focus on the skill enhancement of employees by providing training. Our commitment to excellence in this area is further exemplified by the 5S Excellence Trophy awarded to us by the CII.
Continuous Improvement for Operational Excellence
To drive continuous improvement across our operations, we have adopted the Kaizen methodology to eliminate eight types of waste (Muda’s). Through our online Kaizen portal system, we ensure the successful replication of impactful Kaizens across different locations as a part of horizontal deployment. The categorisation of Kaizens into productivity, quality, cost, delivery, safety, health, and morale (PQCDSHM) based on their impact on performance measurement to achieve operational excellence through the Kaizen journey. In the internal Kaizen competition, we always get maximum participation from the manufacturing function, but now this year we have received a great response and participation from the non-manufacturing function to demonstrate their best practices full of enthusiasm.
24 Nos.
Case Studies in the Kaizen Competition
60 +
QC Stories
(QC Story Competition across Accelo Group)
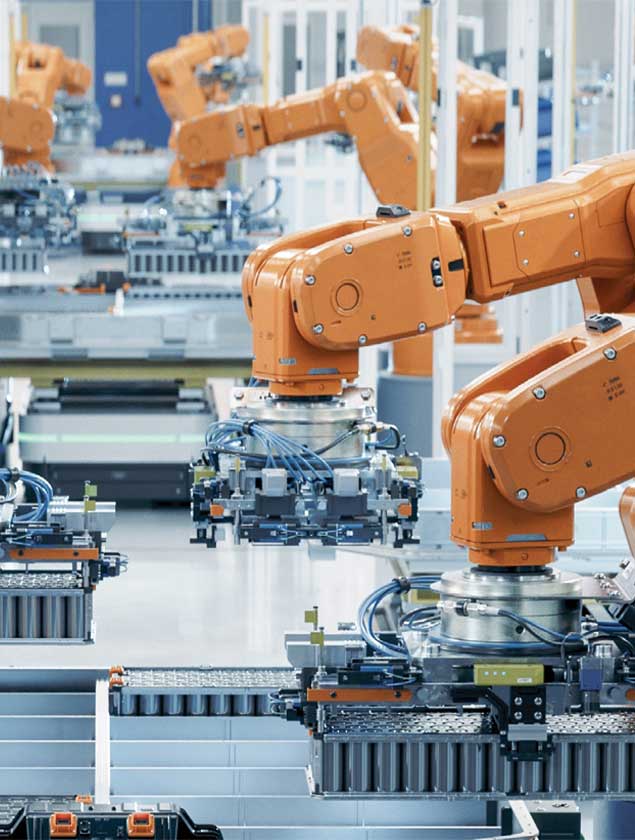
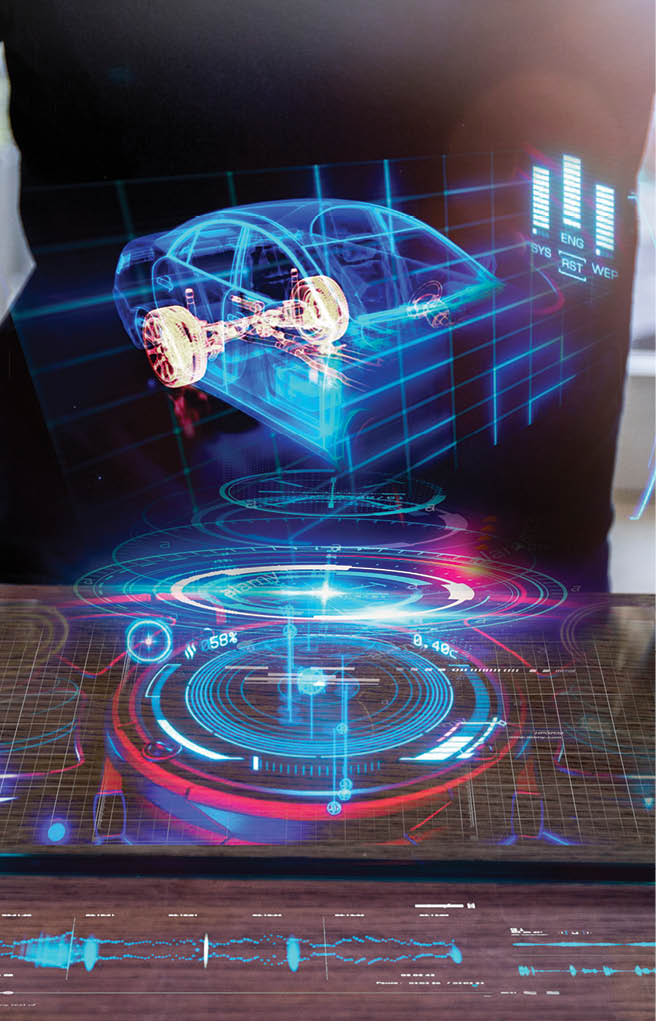
Enhancing Productivity through Visual Management and Controls
Engaging employees in the development and implementation of visual management systems, as part of our Total Productive Maintenance (TPM) efforts, we introduced visual management and controls at our shop floors. In continuation of this, we also displayed the visual boards and signage in the plant covering topics such as safety, 5S, Kaizen, Poka-yoke, TPM pillars, ESG, brand pillars, and policies. This visual approach significantly enhanced productivity and efficiency across our manufacturing facilities.
Ensuring Equipment Efficiency
The TPM philosophy plays a vital role to the journey of manufacturing excellence to achieve ‘4 Zeros’ - Zero Accident, Zero Breakdown, Zero Waste, Zero Defect. Through effective TPM implementation, we achieved optimum utilisation of resources with significant improvements in Overall Equipment Effectiveness (OEE) and operational performance. Our plants are certified for TPM Excellence, and we are striving to achieve the next level of milestones in the TPM journey. We are maintaining high standards of equipment efficiency through collaborative teamwork.
Leveraging MIND™ for Continuous Innovation
At Mahindra Accelo, innovation is at the core of our operations, driven by our proprietary MIND™ (Mahindra INnovation methoD) approach. We have empowered our team to drive innovation and creativity through extensive training and practical workshops. Our focus on innovation is exemplified by our submission for the Mahindra Innovation Award, showcasing our commitment to pushing boundaries and driving excellence in our industry.
Ensuring Quality and Process Efficiency
Our journey with Six Sigma has equipped our employees with the skills and tools to drive quality and process efficiency. The comprehensive training programme based on the Six Sigma Green Belt module has enabled our teams to identify and eliminate inefficiencies, ensuring continuous improvement in our operations.
Prioritising Employee Well-being
Safety is a top priority at Mahindra Accelo, and we have implemented The Mahindra Safety Way (TMSW) model to ensure comprehensive safety practices across all our plants. This proactive approach has resulted in zero reportable and non-reportable accidents, reflecting our unwavering commitment to employee well-being. Our departmental safety score methodology and regular safety audits further reinforce our focus on maintaining a safe working environment. To build & strengthen a safety culture among employees, we celebrate National Safety Week every year. We have focussed on covering safety training on various topics such as behaviour-based safety, fire hydrant system, first aid & CPR, material handling, and electrical safety, among others, by subject expert matter from external faculty. This year, we trained and certified 10 employees for work-at-height training at the Penta-Safe Institute in Lonavala.
National Safety Week Celebrations
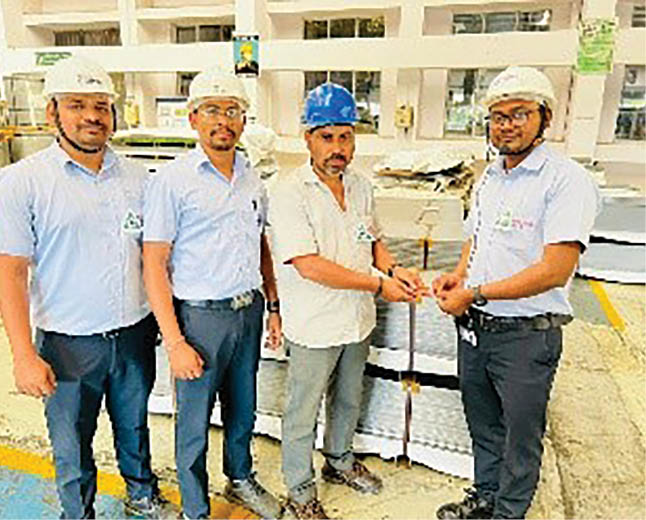
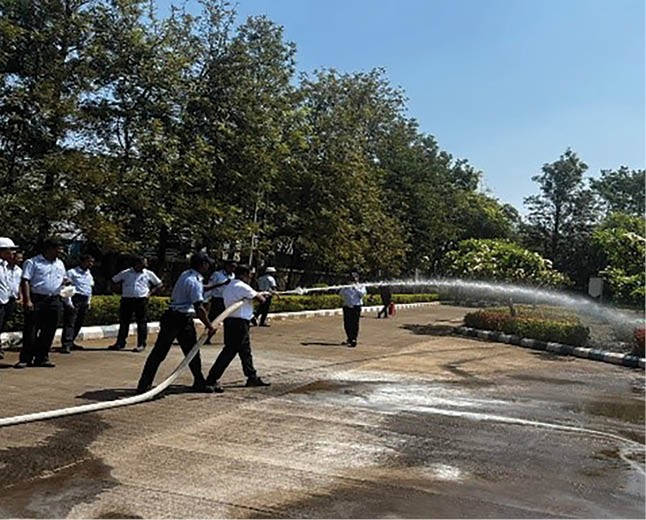
645
Kaizens Completed Across all Locations in FY 2023-24
100%
Participation Obtained for Kaizen Implementation
2
Innovation Projects Completed
61
Improvement Projects/QC Story Completed
217
Trained Green Belts Since 2017
₹ 2 crore+
Cumulative Savings
Upholding Quality, Environment, Occupational Health and Safety Standards
All our plants are certified in ISO 9001:2015, ISO 14001:2015, and ISO 45001:2018, with additional IATF 16949:2016 certifications for specific plants. These certifications reflect our adherence to international standards and our commitment to quality, environment, occupational health and safety.
Streamlining Changeover Processes
The successful implementation of SMED has significantly reduced changeover times in our slitting lines, leading to improved operational efficiency. By adhering to the Elimination, Combine, Realignment, and Simplify (ECRS) principle, we have achieved remarkable improvements in productivity and flexibility.
Driving Operational Excellence
The Mahindra Way (TMW) is our framework for driving operational excellence through systematic and continuous improvement to achieve excellence in the business. Our progress in TMW assessment reflects our commitment towards excellence and our ability to implement best practices across our operations. TMW fosters a culture of excellence in the team for a passionate move to raise our bar in our journey towards excellence.
Ensuring Compliance and Best Practices
We conduct regular safety audits, including TMSW by CSC assessors, IS14489 by DISH-approved auditors, ISO 45001 by TUV Nord, and internal safety audits. These audits help us maintain compliance with safety standards and identify the areas for improvement. Every week, each plant head, along with CFT, takes plant safety gemba round to proactively identify unsafe conditions and prevent potential incidents.
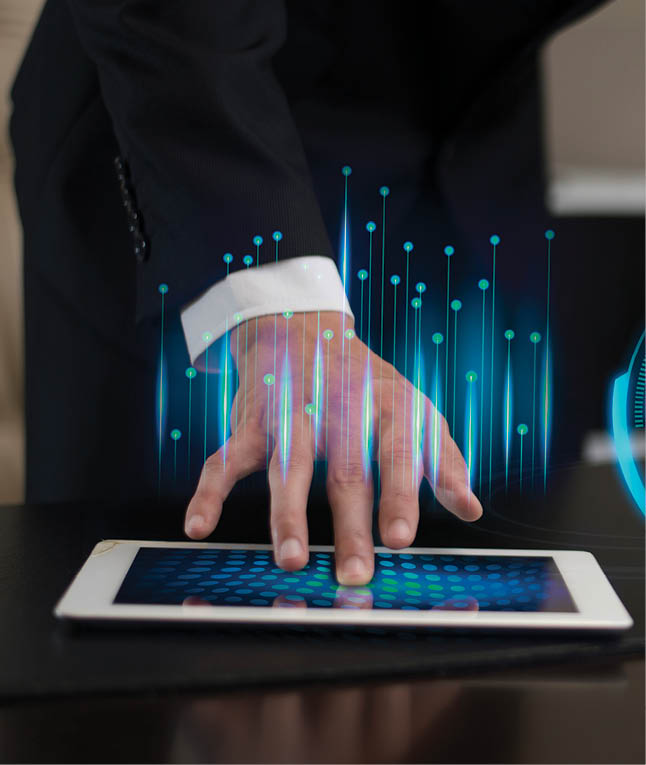
Key Progress Achieved
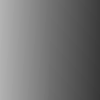
Production Facilities
Our production facilities have been optimised for efficiency and safety, ensuring seamless operations across all our plants.
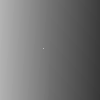
Quality Control
Stringent quality control measures are in place to maintain high standards of product quality and consistency.
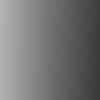
Supply Chain Management
Our supply chain is well-managed, ensuring timely delivery of materials and components to support our manufacturing processes.
Commitment towards sustainability
Commitment towards sustainability involves adopting practices and behaviours that prioritise the long-term health of the planet, society, and economy. This commitment can be demonstrated through various actions taken across the Accelo group. This year we had the assessment of ZWL (Zero Waste to Landfill) by an external agency for our plants. All Accelo plants are now ZWL-certified.
Technological Upgradations
We have embraced technological advancements across our manufacturing facilities to enhance productivity, quality, and safety. These upgrades include the adoption of world-class machinery and the integration of digital transformation. These steps will help Accelo in its journey to be Industry 4.0.
Capital Expenditure Plans and Future Aspirations
Our capital expenditure plans are aligned with our strategic goals of achieving sustainable growth and maintaining our position as a leader in the industry. We continue to invest in modernising our manufacturing infrastructure, enhancing our technological capabilities, and implementing sustainable practices to drive long-term value creation.
Enhancing Efficiency
with Our Digital
Roadmap
Our business processes, supported primarily through manual processes and standalone portals, have served us well till now. But as we move into the next phase of growth, we would need to evolve and build capabilities that enable us to become agile, efficient, and future-ready.
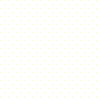
Our Vision
Evolve into a ‘Technology-First Enterprise’ that not only supports the growth plans that are put in place for today but can act as a foundation for unlocking hidden values.
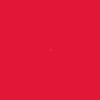
Business Growth: Increase Revenue | Reduce Cost | Increase Operational Efficiency
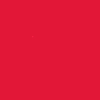
- Manufacturing
Excellence(MES) - Superior Customer/
Employee
Experience - Data Ecosystem
- SAP Audit and
unlocking the
value
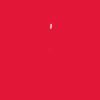
- Smart manufacturing
- Customer Order
Management - Central data lake
- Finance
- Industry 4.0
- Customer
support
automation - Adoption of Al /
ML models - Sales and
Distribution
- Continuous
improvement in
efficiency & quality - Employee
experience
portal - Business
intelligence
automation - HR
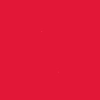
- Customer-
Centric - Function-
Oriented - Data-Driven
- Lean & agile
- Automation &
Standardisation
Our Digital Transformation Journey
In an era defined by unprecedented technological innovation and dynamic market landscapes, our Company has embarked on a transformative journey towards end-to-end digital transformation. With a strategic vision to leverage emerging technologies and drive operational excellence, we are leading a series of ongoing digital projects. These projects encompass Smart Manufacturing, Industry 4.0, Business Intelligence Automation, Central Data Lake, and the Adoption of AI/ML models. Moreover, these initiatives transcend mere technological upgrades; they represent strategic investments to enhance efficiency, agility, and sustainability across all facets of our Company’s operations. Our vision is ambitious yet attainable as we look ahead to the next three years. Our Company aims to emerge as a global leader in the digital age, pioneering innovation and setting new benchmarks for excellence in Industry 4.0. Join us as we navigate this digital odyssey, reshaping the future of our organisation and unlocking new possibilities through the power of digital transformation.
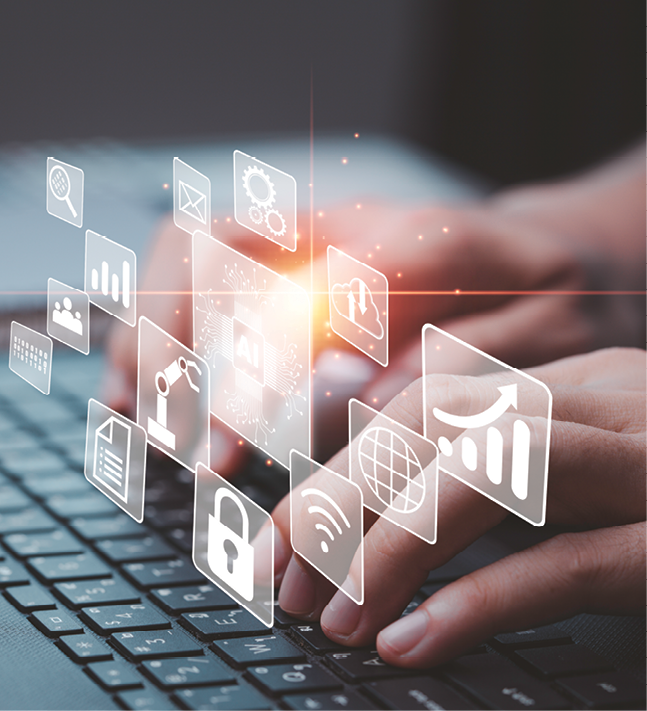
Focus Area
MES Implementation across Plants
Focus
- Partnered with a best-in-industry provider
- MES will seamlessly integrate with our existing infrastructure
- Will create a unified ecosystem that captures, processes, and analyzes real-time data throughout the manufacturing lifecycle
Impact
- Increase operational efficiency by eliminating bottlenecks, reducing manual intervention, real-time monitoring and enhancing overall production speed
- Rigorous quality checkpoints at every stage of the production cycle
- Resource optimisation and cost efficiency by optimising machine utilisation, minimising downtime, and reducing waste
- Agile adaptability with best-in-Industry predictive analytics
- Real-time dashboards and comprehensive reports offering unparalleled insights into production performance
Customer Order Management
Focus
- Implementation of a customer order management system
- Empowers our customers to place orders seamlessly
Impact
- Streamlines the flow of information within our internal systems
- Ensures prompt responses to customer requests, reducing turnaround times and enhancing overall order fulfilment efficiency
- Seamless Integration with SAP and MRP, creating a unified and synchronised environment for more accurate production, planning and execution
Customer Complaints Management
Focus
- Robust complaints management module
- Embracing a more digitised and interconnected approach, we are not just streamlining internal processes but also creating a more responsive and customer-centric environment
Impact
- Address customer concerns promptly, fostering a culture of continuous improvement and strengthening our customer relations
Employee Experience: Success Factors Implementation
Focus
- Aims to revolutionise our human resources practices, fostering a more agile, data-driven, and employee-centric approach across the entire organisation
- Comprehensive solution for end-to-end human capital management
- From recruitment and onboarding to performance management, learning, and development, this platform unifies diverse HR functions, creating a seamless and integrated experience for both employees and HR professionals.
Impact
- Enhanced employee experience
- Data-driven decision-making
- Scalability and future-readiness
- Commitment to employee well-being and organisational growth
Launch of Accelo Konnect - Single Interface for All Employee Needs
Focus
- All employee-related functionalities into a single interface
- Streamline and simplify access to various HR services, tools, and resources, empowering employees to navigate efficiently through their professional journey.
Impact
- Enhanced employee engagement
- Efficiency and productivity boost
- Personalised experience
- Centralised information hub
- Improved HR service delivery
Improving RM Planning: Custom Material Resource Planning Report
Focus
- Implemented Material Requirements Planning (MRP) report, custom-tailored to our organisational needs
- Overcome the limitations of Excel-based planning
- More proactive and informed decision-making
- More accurate, real-time visibility, and the ability to plan proactively for future demands
Impact
- Timely Closure of Open Purchase Orders
- Advanced Raw Material Planning: Horizon extended to a strategic six-month timeframe
- Enhanced Accuracy and Decision Support
- Increased Operational Efficiency
Orchestrating a Data Ecosystem
Focus
- In sync with our transformative initiatives across various projects, we are diligently crafting a robust Data Ecosystem designed to harness the wealth of information generated and optimise it into actionable insights
- This strategic endeavour not only consolidates data from diverse sources but also empowers stakeholders with comprehensive MIS dashboards, revolutionising decision-making processes
- The ecosystem will ensure seamless data flow, eliminating silos and fostering a holistic view of the organisational performance
- Tailored MIS dashboards for business users, offering intuitive visualisations and KPIs, providing real-time visibility into key metrics and performance indicators across all functional areas
Impact
- Informed and Data-driven Decision-Making
- Operational Excellence and Continuous Improvement
- Strategic Alignment and Performance Monitoring
- Increased Visibility
Pushing the Boundaries
with Technology
& Innovation
Embracing innovation as our guiding principle, we continuously strive to redefine possibilities and drive progress in our industry. At Mahindra Accelo, our commitment to leveraging state-of-the-art technologies fuels our pursuit of excellence, whether in developing ground-breaking products or optimising our operations for peak efficiency.
As our Company has expanded and adapted over time, we have undergone a series of transitions, progressing from trading to processing and ultimately creating value-added products. Our relentless focus remains on harnessing technology to propel our ongoing growth and success. Backed by a team of dedicated innovators and fueled by a firm commitment to excellence, we eagerly anticipate the future and are committed to pushing the boundaries within our industry.
Mobility Segment – Moving towards Tier 0.5 Auto Component Player
We take pride in our role as a dynamic and innovative automotive steel supply chain player, continuously pushing boundaries and adapting to evolving market needs. Our Company’s journey began as a steel coil supplier. We have since transformed into a high-end component supplier through strategic investments in product development, cutting-edge machinery, operational efficiency, and a robust distribution model.
Our pioneering spirit led us to establish India’s first merchant blanking line in Nashik, marking our foray into the steel blanking/profiling segment. Focussed on technological advancement and recognising the trend towards thinner and stronger high-strength steel, at Mahindra Accelo, we launched India’s first servo blanking line at Chakan, situated in the western auto hub of India. Additionally, this facility can process up to 1,200 MPA steel and serves as a launchpad for diversification into multiple product lines and OEMs.
Furthermore, our Company’s investment in state-of-the-art progressive stampings, including a new high-strength 1,500-tonne progressive press line at Chakan, has enabled us to attract new OEM customers and attain Tier-1 supplier status. Our latest automotive steel plant in Chennai has expanded our non-M&M customer base, offering an innovative product mix and high-tensile processing capability to meet market demand. Moreover, our Company’s advanced machinery is equipped to handle high-tensile steel, further enhancing our competitiveness in the market.
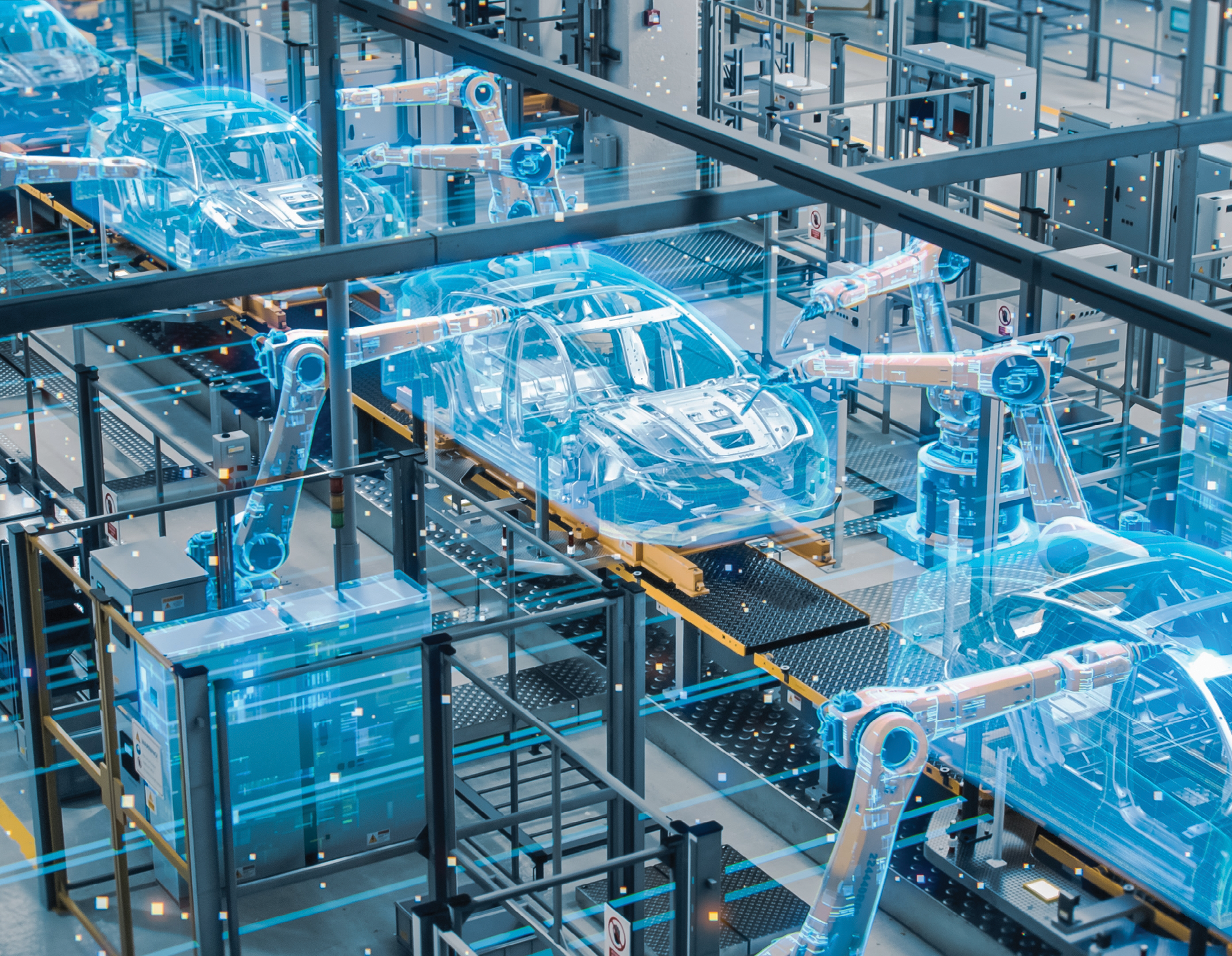
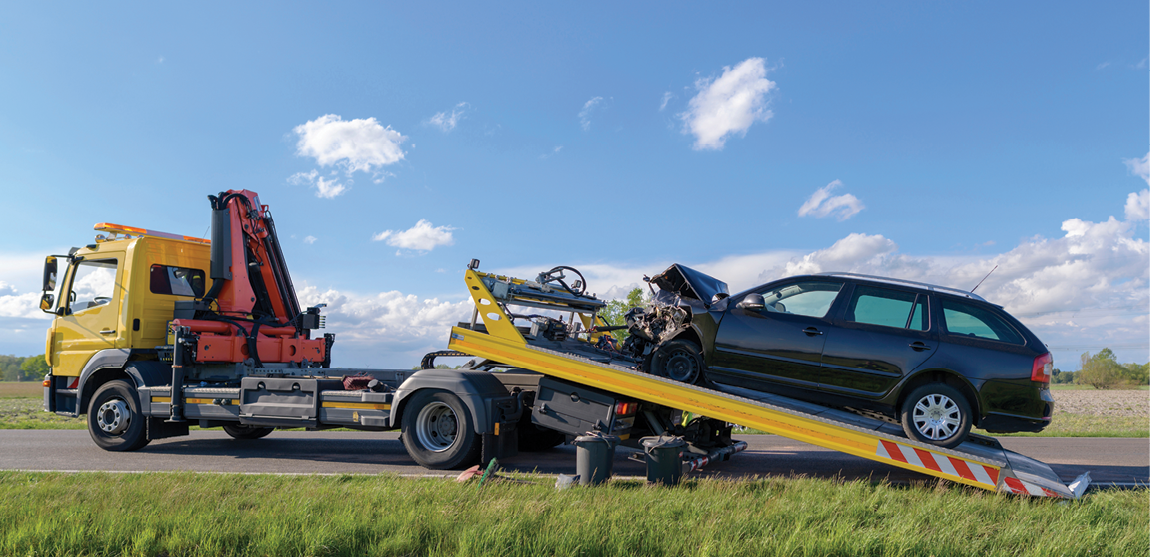
Mobility Segment – CERO – Largest Organised Vehicle Recycler
We founded CERO as India’s inaugural Government-authorised vehicle recycler, making substantial investments to establish our inaugural recycling facility in Greater Noida, equipped with imported machinery. However, in light of the delays in announcing and implementing the scrappage policy in India, we pivoted to an innovative growth strategy for CERO. By localising equipment production to reduce capital expenditure and harnessing the synergies within the Mahindra Group, we successfully expanded CERO’s footprint across the nation. This expansion saw our customer touchpoints surge to 42 locations with a plan to surpass 75+ locations within the next few years.
With the recent unveiling of the scrappage policy by the Government of India and our cost-effective expansion approach, we anticipate witnessing exponential growth in the recycling business segment in the forthcoming years.
At Mahindra Accelo, our goal is to position ourselves as a Tier 0.5 player in the auto component industry and to achieve this, we are making strategic investments in cutting-edge technology. One such investment includes acquiring one of India’s first high-end tandem and transfer presses. These presses can supply skin panels and Class A/B critical components for electric vehicles (EVs) and internal combustion engine (ICE) 4-wheelers. Additionally, this initiative aims to increase our Company’s share of business from existing customers while also enabling us to penetrate new automotive OEMs.
These press lines are versatile and capable of processing aluminium as well, which aligns perfectly with the impending EV revolution. As forward-thinking industry players, we have pioneered the development of fully automatic robotic laser welding lines equipped with Automated Guided Vehicles (AGVs). With these advanced welding capabilities, our Company can deliver critical assemblies to automotive OEMs for both EVs and ICE vehicles.
Furthermore, at Mahindra Accelo, we have made substantial investments in product development to meet the rising demand for EV components. A significant breakthrough in this endeavour is the successful development of EV battery enclosures. Expanding our capabilities beyond steel, we now offer EV battery enclosure components in aluminium. This caters to the lightweight requirements crucial for the EV industry. Through collaborations with global leaders in various aluminium processing operations, such as stamping, forming, welding, deburring, cleaning, and inspection, our Company has delivered prototypes for EV battery enclosures.
Furthermore, at Mahindra Accelo, all our upcoming stamping lines will be equipped to process aluminium, showcasing our commitment to meet evolving customer needs and staying ahead of industry trends.
Energy Segment – Power – Technology & Quality-Led Geographical Expansion and Customer Acquisition
Our innovative approach to product mix in the electrical steel segment (CRGO) has been instrumental in expanding our market presence while simultaneously reducing costs. By offering cut-to-size laminations and value-added products like built-up cores and flux plates, we cater to a broader spectrum of customers, particularly transformer manufacturers. This allows them to concentrate on their core business while also saving on inventory and storage costs.
Our strategic investment in high-speed lines, which is capable of cutting complete transfer logs simultaneously, has facilitated our entry into new markets, notably in Europe, where there is a significant demand for our products. With access to world-class machinery for electrical steel components, a capability shared by only a select few companies in India, we are adept at processing high-grade CRGO steel.
As market leaders in this sector, boasting a total capacity to supply around 50,000 tonnes per year, we are well-positioned for further growth. Additionally, our recently inaugurated state-of-the-art facility in Indonesia offers diverse products, positioning us for a strong foothold in Southeast Asia.
Energy Segment - Electrical Stampings – Entering New Market Segments
Our journey in the electrical stamping business commenced with supplying stators and rotors for electrical motors in the home appliances sector. However, our innovative mindset allowed us to capitalise on our investments and machinery, enabling us to venture into the Electric Vehicle (EV) segment. Today, this segment stands as a key growth driver for MAL, serving both the burgeoning home appliances and electric vehicles industries.
Our unyielding dedication to quality and customer value has been validated by our recent selection as a motor core supplier to one of the world’s largest automobile motor manufacturer, catering to both domestic consumption and exports to European markets. Presently, we supply motor cores and stampings to electric 2-wheelers, 3-wheelers and 4-wheelers, cementing our presence in this rapidly evolving domain.